What is a Spring Finger Contact?
A spring finger contact (SMT) is a small mechanical part used to make connection or grounding on electronic projects. These SMT contacts are made to support harsh environment (humidity, temperature, and vibrations). Spring finger contacts are widely used on on-board electronic projects. Especially for automotive projects (dashboard, headlight) but also on electrical bikes projects (batteries connection), medical applications (sensors) and military project (weapons or vehicles).
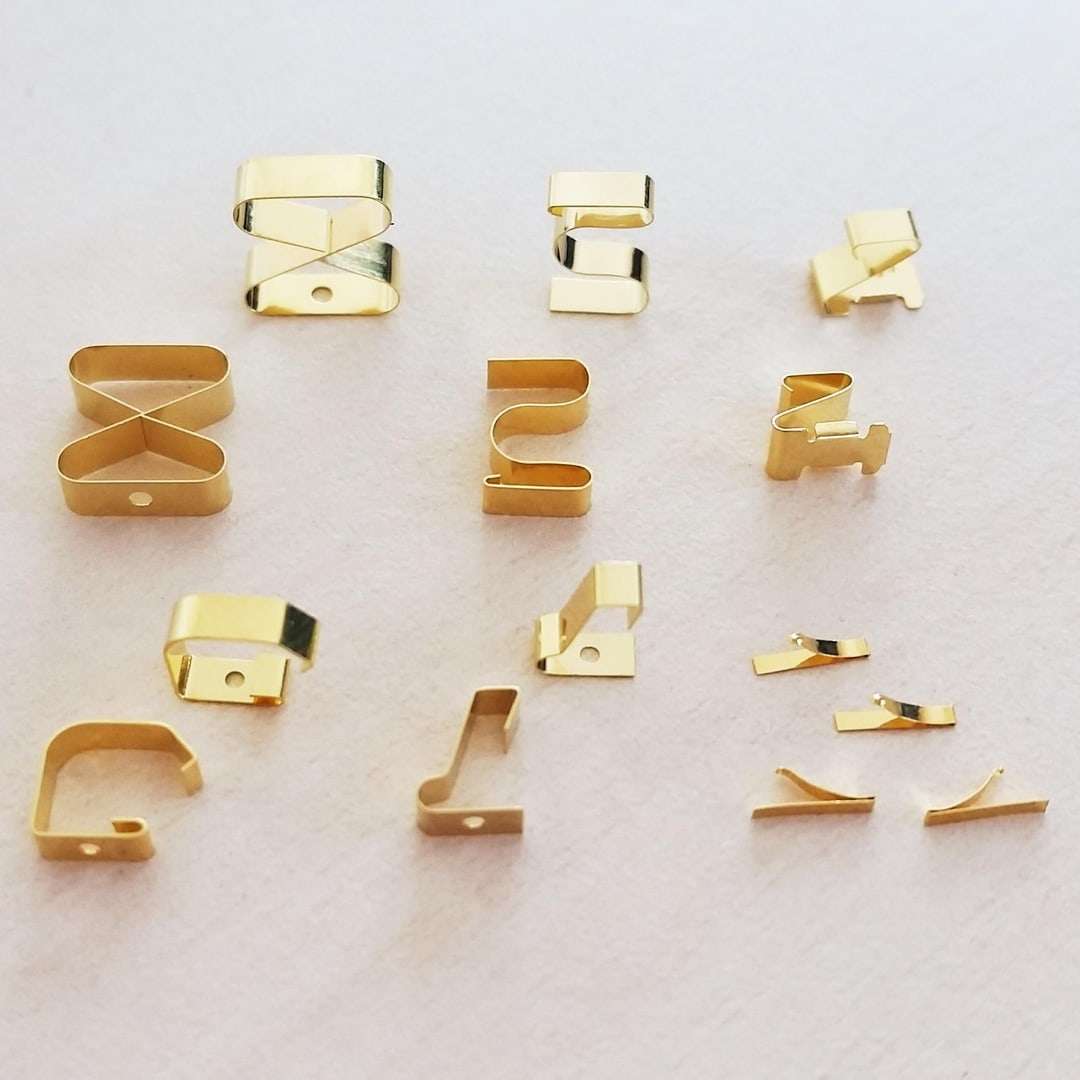
What is the composition of a Spring Finger Contact?
Core materials
Beryllium Copper (CuBe), standard and most common. This material is a kind of bronze alloy.
- Excellent mechanical properties (>300k cycles)
- Good thermal conductivity
- Good electrical conductivity (electrical resistance is a few milliohms)
- Easy forming
Stainless steel, less common (due to lower mechanical properties)
- Lower mechanical characteristics than Beryllium Copper (CuBe)
- Lower electrical conductivity
- Cheapest than CuBe material
Other metals and alloys can be used. However, not using standard material might lead to higher costs and worst characteristics (as electrical than mechanical characteristics).That is why we recommended to use as much as possible Copper and Beryllium (CuBe) as core material for your spring finger contacts (for standard contacts as well as for your custom parts).
Inner Electroplating (mandatory/standard):
Ni (Nickel)
- Protect the inner core (CuBe) from oxidation
- Ensure a high adhesion force between the electroplating layers (with the optional gold electroplating for example)
- Withstand high friction level
- Good weldability on PCB
External surface treatment (optional) :
Au (Gold)
- Higher resistivity to bad exterior environment (humidity, temperature)
- Higher conductivity (gold is a highly conductive material)
Sn (Tin)
- Good weldability
- Poor resistance to oxidation, especially in high humidity environment
Other electroplating possible on demand
We strongly suggest to use standard as much as possible
About Optional Surface Treatment
The spring finger contacts can be delivered without surface treatment on the outside (Au/Gold plating). Indeed, the price of the raw material (gold) is high and volatile comparing to the raw material CuBe (Copper Beryllium) used for the core of the spring contact. In some cases (depending on the volume and the design), the gold surface treatment can even double the cost of the spring finger contact (due to the raw material cost).
How are spring finger contacts made?
The manufacturing of spring finger contacts starts with metal strips of several thousand of meters of Copper Beryllium (the raw material for the core of the spring contact). The thickness of the strip is 0.08mm or 0.1mm depending on the design of the spring finger contact.
Then this strip of material goes into a specific machine with tens of tools arranged in circle. Each tool does a specific operation (a blending, a cut, or a fold) in a specific order.
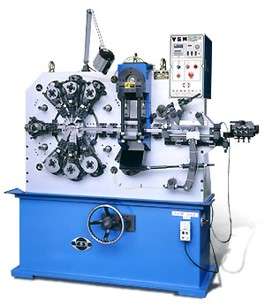
Firstly, with Nickel (Ni), and if required, with gold (Au).Once the spring finger contact is electroplated,it is packaged on reel for assembly on SMT process (automatic assembly on PCB).
The standard global lead time from order to delivery is 8 to 12 weeks (if there is no stock). That is why you should anticipate as much as possible all of your electronic project using this kind of spring contact. Lead time can be reduce for standard spring finger contacts on stock.
Mass production of these contacts requires mass production tooling. In the case of standard contacts, there are no tooling or start-up costs (the tooling already exists).
In the case of custom mass-produced contacts, a contribution to the cost of manufacturing the production tooling is required. For prototyping, it is possible to manufacture a few dozen parts without production tooling. In this case, we use temporary tooling (or soft tooling). This temporary tooling makes it possible to produce a few parts without additional tooling costs. However, the unit cost of the part will be higher because of the limited efficiency of the tooling in terms of production time. For the production of a batch of prototype parts, the standard lead time between order and delivery is 4 to 6 weeks.
Spring finger contacts are widely used in many areas of electronics. On-site production is IATF 16949 certified (strict automotive standard) and processes are ISO 9001 certified. The final spring contacts comply with RoHS and Reach standards.
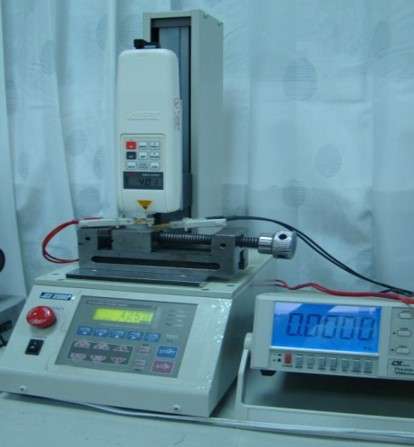
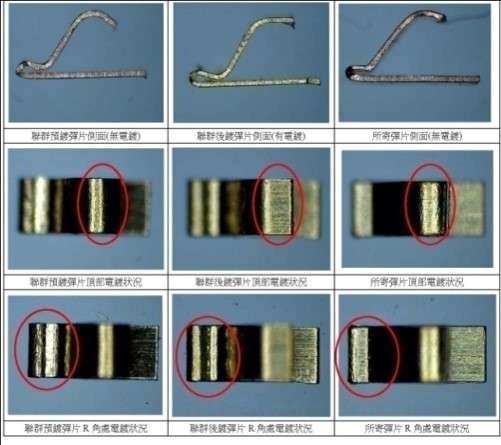
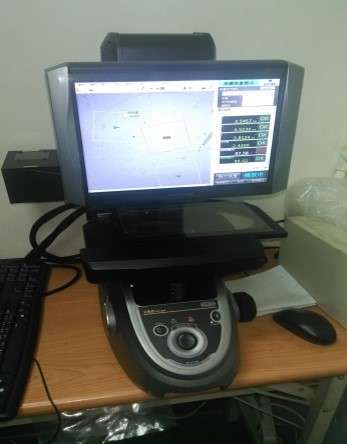
Conflict minerals are materials mined in areas of armed conflict and human rights abuses, such as tantalum (Ta), tin (Sn), gold (Au) and tungsten (W). Profits from the sale of these minerals financed the continuation of fighting during the war. Control of the lucrative mines also became an object of combat. As a global citizen, Compelma supports human rights and fulfils its corporate social responsibility. We continue to pay attention to this issue and exercise due diligence to ensure that Compelma and Compelma’s suppliers do not use any of these conflict minerals.
Why are spring finger contacts (SMT) used ? :
Spring finger contacts are ideal for making low-voltage electrical connections on printed circuit boards (PCBs). They are easy to use, particularly because of their compact size and automatic installation (SMT). Spring finger contacts can be used for antenna connections, earthing or the prevention of electromagnetic noise or static electricity.
Battery contact
For electric bikes
Consumer equipment (household appliances)
Cameras (cameras, on-board equipment, drones)
Mobile phones
Grounding
Contact between PCB
Contact between PCB and chassis
Vibration-resistant connection
Automotive dashboard
On-board equipment
Antenna spring connection
Mobile phone antenna
GPS antenna
Automotive antenna
Vibration-resistant connector
Automotive equipment
Military projects, equipment and weapons
Aeronautical equipment and sensors
“Plug and Play” configuration
Modular connection
Battery connection
Electromagnetic shielding of cables
How are spring finger contacts (SMT) used?
Spring finger contacts can be used in a variety of configurations. Depending on the shape and design of the spring contact, the electrical contact is made vertically or laterally on the PCB.
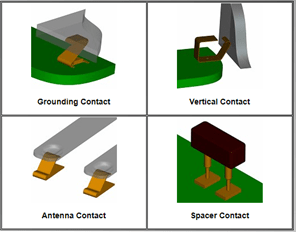

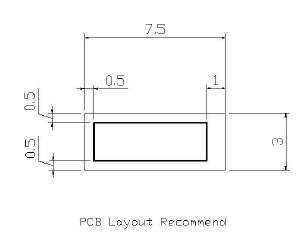
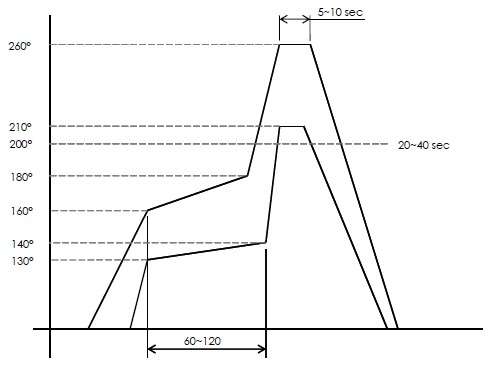
What are the limits of spring finger contacts (SMT)?
The thickness of the strip of CuBe material used to manufacture these parts is 0.08 or 0.10 mm (depending on the design of the spring finger contact). As a result, these spring finger earth contacts cannot withstand a high current or voltage. We recommend that you do not exceed 3A/piece. These spring finger earth contacts are also sensitive to violent (rapid and high) variations in voltage or current.
The height of the largest spring contact is 13mm as standard. This height is limited by the weight of the part and the constraints imposed by automatic installation (SMD installation). Some customised spring finger contacts can go beyond this height. For example, we have developed a custom contact with a height of 22mm (used on an automotive project and a medical application).
From a mechanical point of view, the maximum compression for spring finger contacts is 40%. For custom spring contacts, using a thicker material (e.g. 0.15mm), the recommended compression ratio may be less than 40%. If the material is thicker, the spring’s elasticity will be less than with a thinner material.
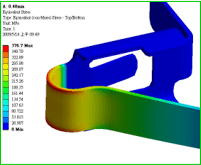
How do you sum up spring finger contacts?
Spring finger contacts are an alternative to EMI gaskets (filled silicone or metal seals) for electromagnetic or radio-frequency shielding and grounding. These spring finger contacts are also used as connectors. Spring finger contacts are designed to optimise manufacturing processes. These spring contacts are compatible with SMD installation and are packaged on reels (7″ or 13″ depending on the spring contact reference).
The design of the spring finger contacts gives greater flexibility to electronic projects. Especially for projects with stringent space and weight requirements.
Most spring finger contacts (SMDs) are made of copper-beryllium (CuBe), with a standard internal surface treatment of nickel (Ni), then electroplated with gold (Au) (optional). These surface treatments on the spring-mass contacts offer a number of advantages:
– Improved electrical conductivity
– Greater resistance to humidity and high temperatures
– Better solderability on the PCB
The design of the spring finger contact can be standard or customised according to your specifications and constraints.
What about spring finger contacts for your electronics project?
Yet it seems that every time you need spring finger contacts, you have to search through a million different references to find the right one. And once you’ve found it, they may not be right for your specific application.
That’s why Compelma is here to meet all your spring contact needs. We have a wide selection of contacts that have proven themselves in many industrial fields and electronic projects. What’s more, our production capacity means we can take you from prototyping to mass production. For example, we are suppliers to some of the world’s largest automotive OEMs (large volumes of standard parts) as well as military manufacturers using small quantities of specific spring contacts. To complement our standard range, we offer a wide range of customisation options so you can get exactly what you need for your electronics project.
We can supply prototype mass-produced contacts using soft tooling. This allows us to manufacture validation parts without tooling costs. On the other hand, the price per part is higher because of the slower production speed.
This process is ideal for enabling you to validate your design before incurring tooling costs for mass production, and to obtain a much more competitive price per part.
Do you have a question about spring finger contacts for your application?
You can get in touch with us using the chat or by sending us a message using the contact form just below. Let’s talk about spring finger contacts!