Why use an EMI and/or IP gasket in an electrical assembly?
The primary aim is to ensure a seal against :
– To particles (dust)
– And/or fluids (air, water)
– And/or electronics (grounding) in the case of EMI (electromagnetic compatibility) shielding joints.
This water resistance is assured between two moving parts of a piece of equipment. For example, between two parts of an assembled electronic box, between a closet door and its frame, or around the periphery of the cover of a piece of equipment.
Sealed against fluids and particles – IP rating
The level of impermeability of electrical equipment to fluids and particles is indicated by its IP level (Ingress Protection). This protection index is standardised by the International Electrotechnical Commission.
It is made up of the letters IP followed by two digits (or one letter in certain specific cases). The 1st number indicates protection against solids (particles and dust). The 2nd number indicates protection against liquids. To comply with the standard, tests must be carried out with water.
For example, an IP68 certified equipment is completely dust proof and waterproof to a specific depth and time duration specified by the manufacturer.
For more information, you can consult the Wikipedia page on the subject.
Now let’s get down to business!
Electromagnetic sealing: Grounding
In addition to fluid proofing, the gaskets can be made of an electrically conductive material to provide an electromagnetic shielding through grounding. What is electromagnetic shielding and electromagnetic compatibility (EMC)?
Many fabrication methods make it possible to manufacture conductive gaskets:
– Using a metal particle charged silicone (Nickel and Carbon [Ni/C] or Silver and Aluminium[Ag/Al])
– Drown a metal mesh in silicone (Monel or aluminium type)
– Surround the joint with a conductive material (for example metallized fabric [Ni/Cu/Ni], therefore conductive)
These different methods of gasket manufacturing ensure a shielding level up to 120dB for EM(electromagnetic) and RF (radio frequency).
Integration of EMI and IP gaskets in an electronic assembly
To achieve high performance levels, the gaskets must be properly integrated into the electronic design. This integration must be considered at the beginning of the project.
For example, to ensure IP68 sealing and ground continuity around an electronic enclosure’s periphery: a groove must be designed to integrate the gasket. Without this groove, an IP68 level is difficult to achieve.
Several solutions exist to compensate for the detection of leaks in a piece of equipment after its conception. However, these methods are still not optimized and so not recommended. Indeed, the performance levels can only be lower.
For example: Foam gaskets surrounded by a conductive fabric allow grounding on openings or at certain locations of a piece of equipment (around a connector for example). These gaskets are placed directly on the metallic surface and are held in place by an adhesive. A groove is therefore not necessary. However, there must be enough space in the design.
If a high IP sealing is required, conductive foam gaskets are not suitable. The conductive fabric around the polyurethane foam stops dust particles and some droplets, but shows its limits in a more demanding environment.
Beware of compressive forces
In addition to the expected level of tightness, particular attention must be paid to the compression forces in the electronic assembly. If the EMC shielding gasket is too hard or oversized, your assembly risks being damaged by unanticipated mechanical stresses. On the other hand, if the conductive seal is too flexible, too compressed or undersized, it is likely to degrade rapidly (deformation or even tearing) and the EMC and/or IP seal will no longer be guaranteed.
Some examples of EMI shielding gaskets
Foil over Foam (FoF) EMI shielding gaskets:
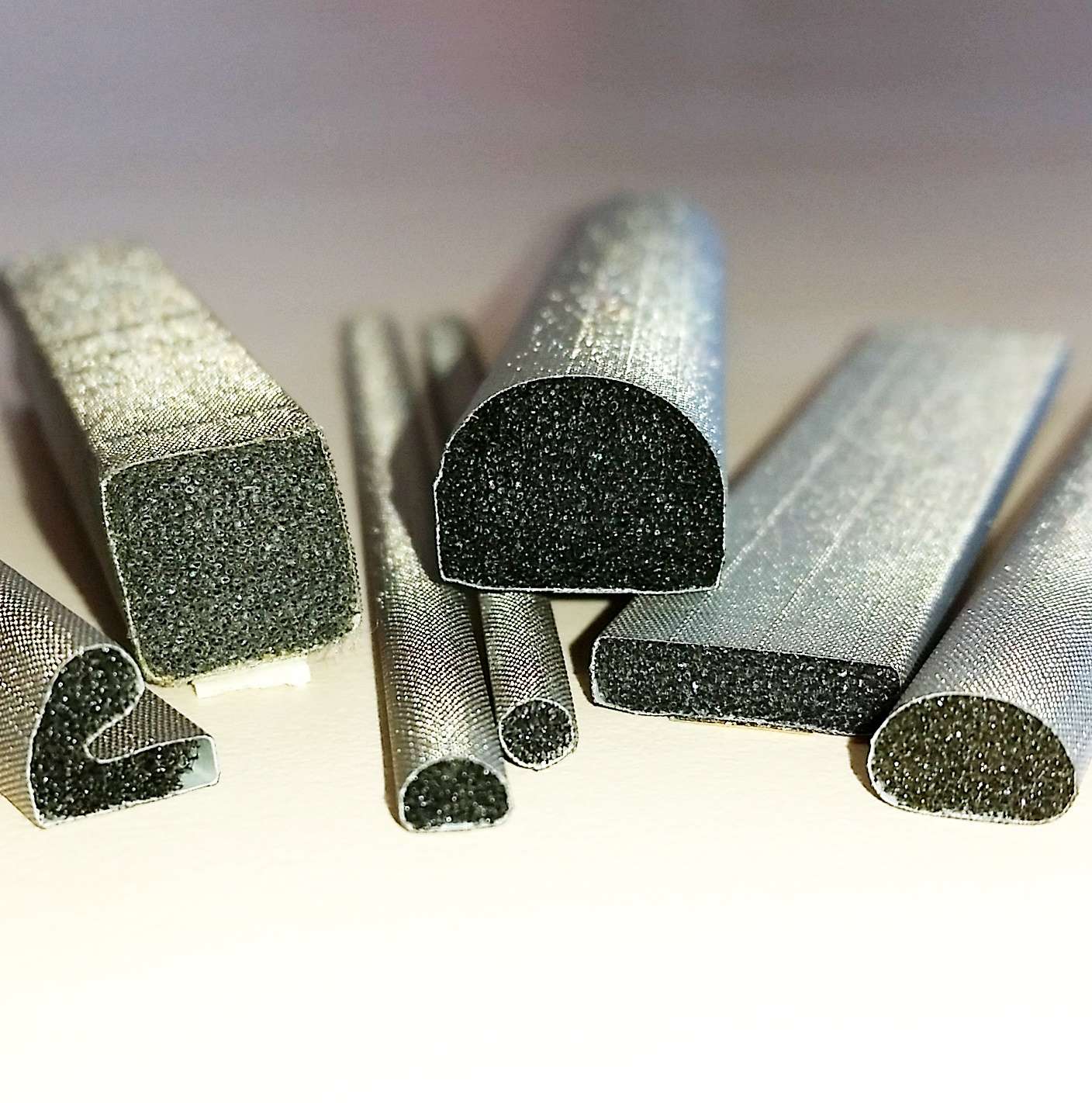
These EMI shielding foam gaskets require low compression forces (due to the polyurethane foam). They can therefore be used in lengths of several metres without too much mechanical stress. These EMI shielding gaskets also have good mechanical resilience and withstand abrasion and compression/decompression cycles. They are therefore suitable for RFID cabinet door openings, for example.
EMI shielding gasket using conductive silicone (Ni/C or Ag/Al filled) :
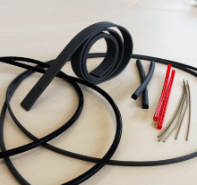
The metallic particles in the silicone make it harder than a neutral silicone (but conductive). Therefore an EMI shielding gasket made of charged silicone will be hard (hardness > 60 Shore A). The design of the assembly and the compression forces will have to be adjusted accordingly. For example by increasing the number of clamping screws along the gasket. Bi-material EMI silicone gaskets are an excellent alternative for reducing the required compression forces.
Metallic EMI shielding gaskets
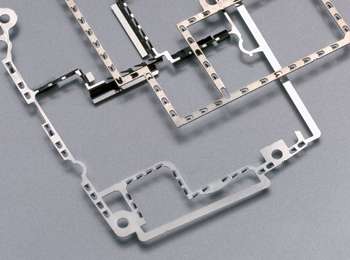
These metallic gaskets for EMI shielding are made from a 0.15mm thick metal sheet (Sandvik Chromflex). The spring teeth protrude from the gasket by 0.5mm. This gives an overall gasket height of 0.2mm and 0.15mm in maximum compression. The compression force for this type of gasket is minimal.T he teeth are easily compressible.
To avoid the risk of over-compression of EMI shielding gaskets you need to be able to control the compression of the EMC gaskets. Either by controlling the tightening torque or by adding mechanical stops.
Choice of materials for EMI shielding gaskets
The choice of materials must be taken into account when selecting the type of EMI shielding gasket. Not only for electrical conductivity and EMI shielding performance, but also for compatibility with its environment. Galvanic couples are important to ensure the longevity of an equipment. Some metals, in a salty environment, will react with each other and oxidize rapidly.
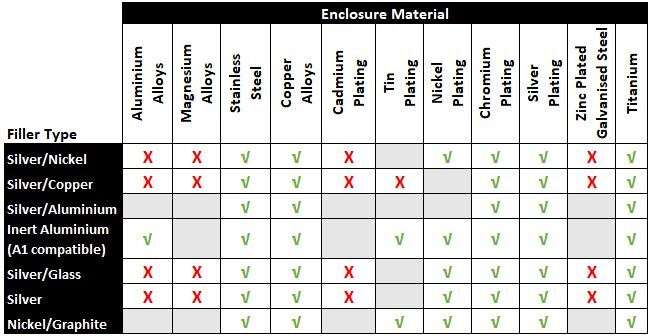
For example, Ni/C (Nickel Graphite) loaded EMI gaskets are recommended when mounted on a nickel surface (plated or painted) enclosure. On the other hand, a silver or copper loaded gasket in contact with an aluminium housing in a salty environment will corrode quickly. This will result in mechanical degradation of the seal, with a loss of EMC and/or IP sealing. In addition to corrosion on the worst case.
Grounding with the EMI shielding gasket
To be functional, the EMI shielding gasket must be grounded. This grounding must be made directly against the metal. Some coatings or paints are electrically insulating. In this case, be careful to ensure that the earth is picked up by a tin on the paint or surface coating, which allows contact between conductive surface and conductive surface.
Some surface coatings are conductive. For example, for aluminium surface coatings (on a heat sink, for example), Surtec 650 is electrically conductive, as opposed to anodising, which is insulating.
Lifetime of an EMI shielding gasket and maintenance
The shielding effectiveness of an EMI gasket in place varies very little over time (except in the case of oxidation or failure to respect galvanic couples). However, if maintenance is carried out on the equipment and the EMI gasket is dismantled, care must be taken.
During a dismantling operation, the seal may come out of the groove or move. In this case, depending on its level of resilience (its ability to return to its original shape), electromagnetic shielding and IP sealing may be affected.
We recommend changing EMI gaskets (especially filled silicone or foam and conductive fabric versions) at each maintenance operation to avoid a second maintenance operation after reassembly of the equipment and detection of an EMI or fluid leak due to the seal.
Friction resistance is also a consideration in certain applications. EMI foam gaskets with conductive fabric are particularly resistant to friction and wear. These conductive gaskets are therefore suitable for electromagnetic (EMC) and radio frequency (RF) sealing of cabinet doors or between two sheet metal parts.
In all cases, and for all types of seals, we recommend regular inspection of equipment and seals, and replacement if necessary. It is better to replace a seal than to have to carry out maintenance following a system failure.
What determines the shielding effectiveness of an EMI shielding gasket?
The level of EMI shielding does not depend solely on the materials chosen. Performance is all about finding the best balance between integration, price, maintenance and material compatibility. Let us help you choose your EMC seals to ensure a high level of electromagnetic shielding (EMC) and/or IP sealing performance.
To help you see things more clearly, we have listed the characteristics of the different types of EMI shielding gaskets available. You’ll notice that no solution is perfect. Before making your choice, contact us to validate the shielding technology.
You can also get in touch with us right away via chat or the contact form at the bottom of the page. 😃
Charged silicone EMI gaskets
These are elastomeric (silicone) seals. Silicone can be loaded with metal particles to make it conductive and thus provide electromagnetic shielding through its electrical conductivity. A filled silicone is harder than a neutral silicone (around 65 Shore A for a conductive silicone compared with 40 for a neutral silicone). A fluorosilicone type silicone can also be used to ensure better resistance over time to solvents and hydrocarbons.
EMI gasket material :
Filled silicone (Ni/C or Ag/Al) and/or neutral silicone. Fluorosilicone variant for demanding applications (such as medical or military applications).
EMI Gasket shaping processes :
Silicone gaskets for EMC and/or IP can be manufactured by extrusion to a standard or custom profile (expect to pay a few hundred euros for a custom extrusion profile with a lifetime guarantee). Extruded EMC and/or IP silicone gaskets can be supplied by the linear metre or cut to length.
These gaskets can also be cut from a sheet of conductive silicone to obtain a flat gasket.
Variant 1: Bi-material EMI gaskets
(neutral silicone and conductive silicone)
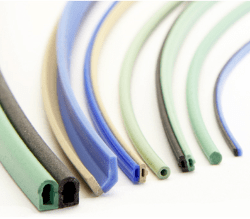
Bi-material silicone EMI shielding gaskets can be manufactured by simultaneously extruding two types of silicone: a filled silicone (Al/Ag or Ni/C) and a neutral silicone (fluorosilicone or not). The advantage is the flexibility of the EMI shielding gasket compared with a pure filled silicone gasket (which is harder). The arrangement of the two types of silicone on the joint profile varies according to the specifications to be achieved. You can find out more about these bi-material EMI shielding gaskets on the corresponding webpage.
Variant 2: Neutral silicone weft gaskets
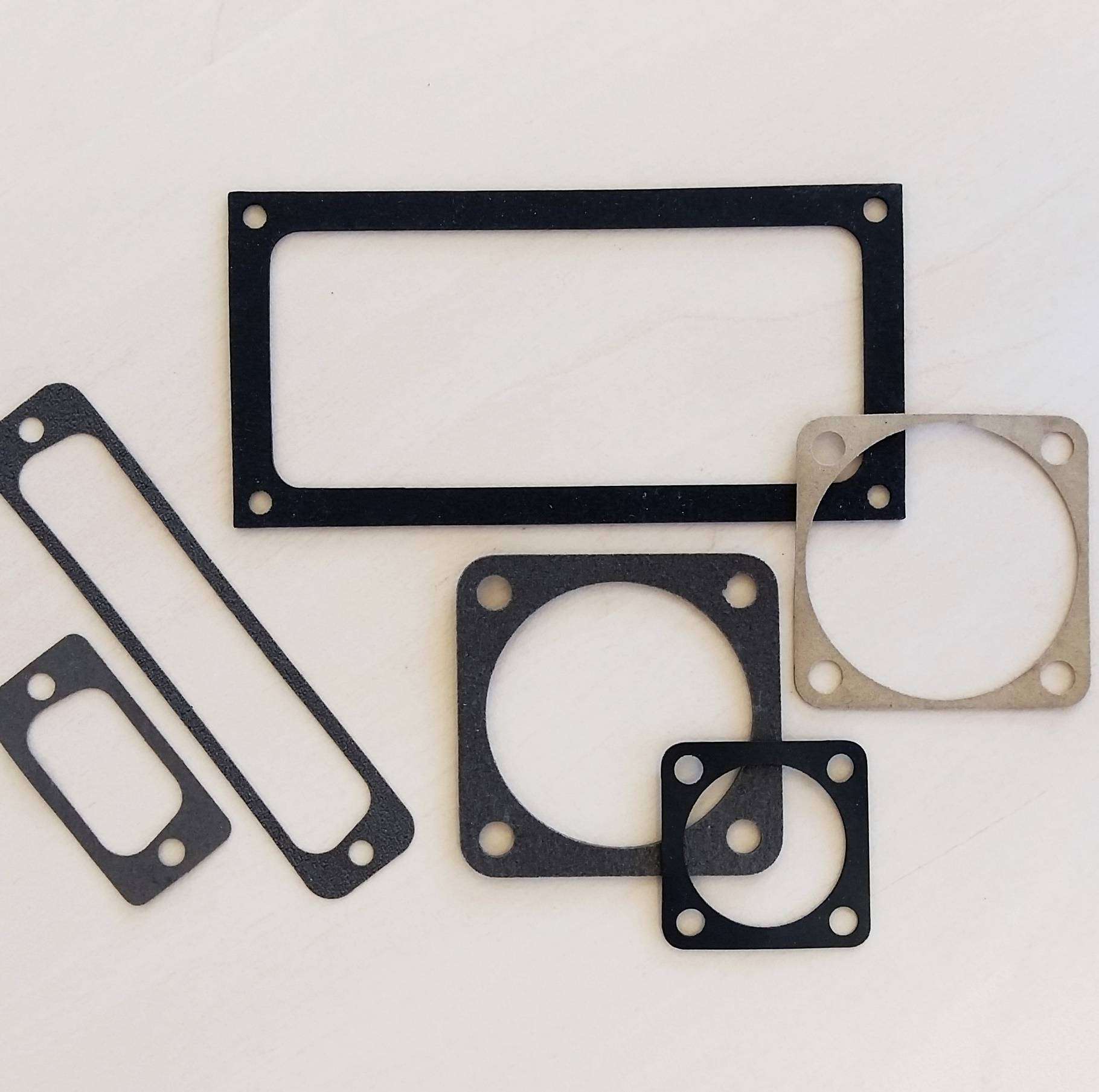
For certain demanding projects (nuclear, military or medical), a metallic mesh is added to the neutral silicone to make the EMI gasket. The advantage is that the flexibility of neutral silicone is retained, while the electrical conductivity of the metal is added by the metal mesh. The metal mesh is added in the silicone during manufacturing (usually monel or aluminium). This type of gasket has excellent resilience and durability. It is only manufactured by moulding or plate cutting.
Seal tightness level :
These seals (conductive or non-conductive) provide very high levels of tightness against fluids and particles (up to IP68 or IP69). The highest levels of fluid tightness are achieved when the seals are arranged in a groove.
We can help you choose the dimensions of the seal (profile and length) to match the design of your groove, or vice versa.
Compelma’s notice :
These EMI gaskets offer an excellent compromise between performance, cost and durability. We have a good deal of leeway when it comes to shaping and designing this type of gasket. This makes them very good candidates for most electronic projects.
Metallic EMI shielding gaskets
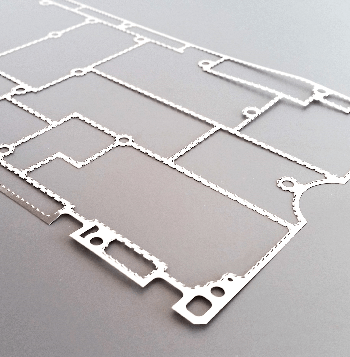
Metallic EMI shielding gaskets are manufactured by chemical cutting and then mechanical forming from a 0.15mm thick steel plate (Sandvik Chromflex). These EMI shielding gaskets have a series of small spring-loaded teeth all round the periphery. This enables them to compensate for any play due to tolerances between two metal castings, for example.
EMI gasket material :
Sandvik Chromflex metal foil, 0.15 mm thick
Joint shaping process :
You provide a 3D drawing of the contours of the EMC shielding joints. On this basis, we will make a proposal for the positioning of the spring teeth along the EMI gaskets. Prototypes are manufactured using prototype tooling (soft tooling). Mass production tooling is then required for larger volumes. These EMI shielding gaskets are only made to measure.
Seal tightness level :
These types of EMI shielding gaskets are, by definition, designed solely for EMI shielding by providing a ground connection between two foundries. There is no efficient sealing against particles or fluids (IP).
Compelma’s notice :
These EMI shielding joints are widely used in microwave and hyper frequency shielding. In particular, they are used by major manufacturers in the telecoms, military and medical sectors. The launch costs imposed by the nature of the EMI gasket are more easily amortised over volumes of several dozen parts minimum.
Foil over Foam (FoF) EMI shielding gaskets
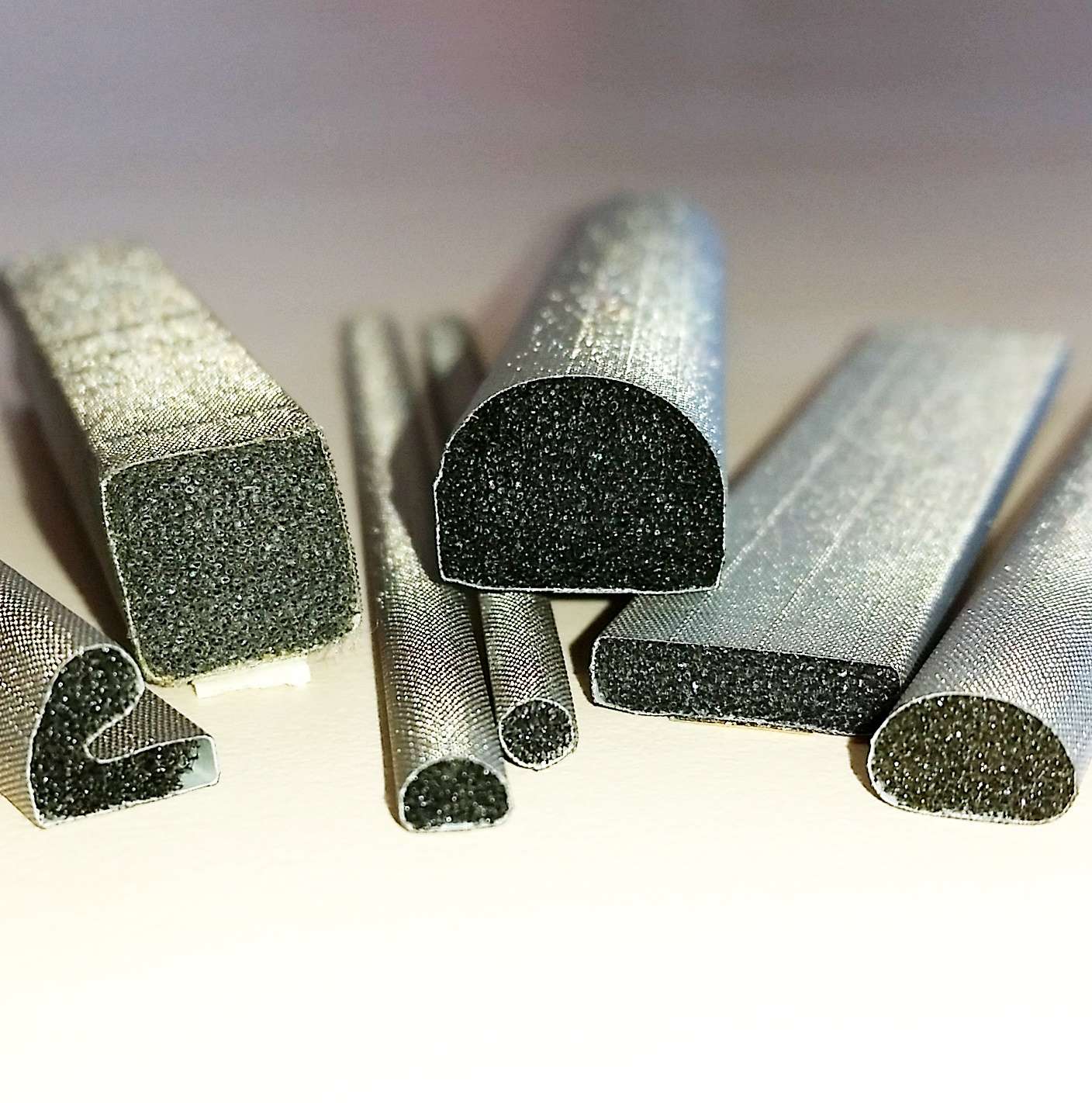
These EMI shielding gaskets are economical and easy to use in most electronic projects. Conductivity is ensured around the entire periphery of the gasket by the conductive fabric. The metallisation (Ni/Cu/Ni) applied to the polyester fabric guarantees very good resistance to abrasion (in the case of EMC shielding on a door opening, for example). The polyurethane foam body ensures good mechanical behaviour and resilience.
Gasket tightness level :
These EMI gasket are easy to use and to integrate (no need for a groove) but provide a limited sealing level against fluids and particles. However they support numerous number of compression cycles (as for a door application application).
We can help you choose the dimensions of the seal (profile and length) to match the design of your groove, or vice versa.
Compelma’s notice :
These EMI gaskets offer an excellent compromise between performance, cost and durability. We have a good deal of leeway when it comes to shaping and designing this type of joint. This makes them very good candidates for most electronic projects.
EMI contact strips and EPDM seals with metal mesh: Obsolete EMI shielding technologies
These two types of EMI shielding products are still available on several electronic distributor websites. However, these EMI products are obsolete; you can obtain much better results with other products for the same price and with a better resistance over time.
For example, copper or stainless steel EMI shielding contact bars do not stand up well to repeated compression cycles. Some of the teeth may break as a result of wear, with a significant impact on the product’s lifespan. These EMI shielding bars are also permeable to dust and are very sensitive to oxidation (especially the copper versions). As for EMI shielding gaskets in EPDM with a metal mesh, they look homemade compared with gaskets in filled silicone (bi-material or standard). The cost is also more competitive for EMI shielding gaskets in filled silicone.
Limit of EMI shielding gaskets
The gaskets we have discussed are designed for EMI sealing in the microwave range (metallic gaskets), RFID (foam gaskets with conductive fabric) or Radio Frequency more generally. However, these seals are not suitable for low-frequency electromagnetic shielding (10kHz – H field). These magnetic fields are only stopped by gaskets with a high ferrous (iron) load. This is because the EMI shielding gasket must be magnetic in order to control and/or direct the magnetic fields. Mu-metal (μ-metal), an alloy of iron and nickel, is used in particular for projects with magnetic fields. Compelma does not offer this material or seals for magnetic shielding.
How do I choose a shielding gasket for my EMI?
A detailed article on EMI shielding seals that can be summed up in a single sentence:
Get advice and support from a professional.
He will be able to share his experience with you on the choice of materials and applications.
Each EMI gasket application is too specific to provide a generic solution. The type of application, the integration stage, the environment, the sector, the technical requirements. These are all parameters on which a professional can help you see things more clearly. Supporting you from the earliest stages of your design also means you can approach testing and certification with peace of mind. By having confidence in the materials you have chosen and their level of performance. For example, by avoiding silicone-based materials in space or medical applications (because of the risk of outgassing) or by mixing galvanic couples in a saline environment.
Why choosing Compelma?
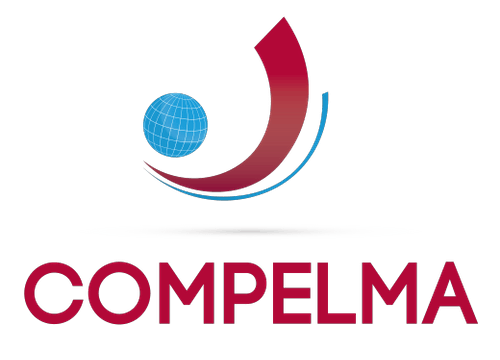
More than 80% of our products are tailor-made using technologies and processes that we master. Our aim is always to offer the most suitable EMC shielding parts within budget.
With over 30 years’ experience and advice, we’re happy to work with you. On new projects, or in the search for alternatives or obsolescence.
Gore has placed the GS2100 material on the obsolescence list. However, this material was qualified for many military projects, which are still deployed and require maintenance. Compelma was asked by its customers to propose an alternative material, with the same technical characteristics, to replace GS2100. After consultations and discussions with our suppliers and partners, we developed the alternative material: COECE2110. This Compelma material has since been qualified on the projects concerned and is supplied on a regular basis.
You can contact us (Florian, Li or Clément) by chat for a live answer, or by using the contact form.
Thank you for reading this article to the end. See you soon !⚡
Clément for Compelma